O acompanhamento contínuo das condições físicas de equipamentos que fazem parte da cadeia produtiva em qualquer subsetor da indústria de óleo e gás é pré-condição para a manutenção do bom funcionamento do negócio, seja através do planejamento de novas frentes, pela implementação e manutenção das operações em andamento ou pela garantia do descomissionamento seguindo as premissas regulatórias.
Risco para Operação
Ocasiões de paradas não programadas são, muitas vezes, resultados de “apostas” feitas por gestores sobre equipamentos confiáveis e processos estáveis por vezes suscetíveis a erro humano ou ao tempo em que os equipamentos estão operando. Essas “apostas” podem gerar diversos tipos de prejuízo para a companhia como um todo.
Uma pesquisa feita sobre 125 empresas dos EUA no último trimestre de 2022 reporta um prejuízo financeiro médio de US$ 108.708,00 resultante de paradas não programadas.
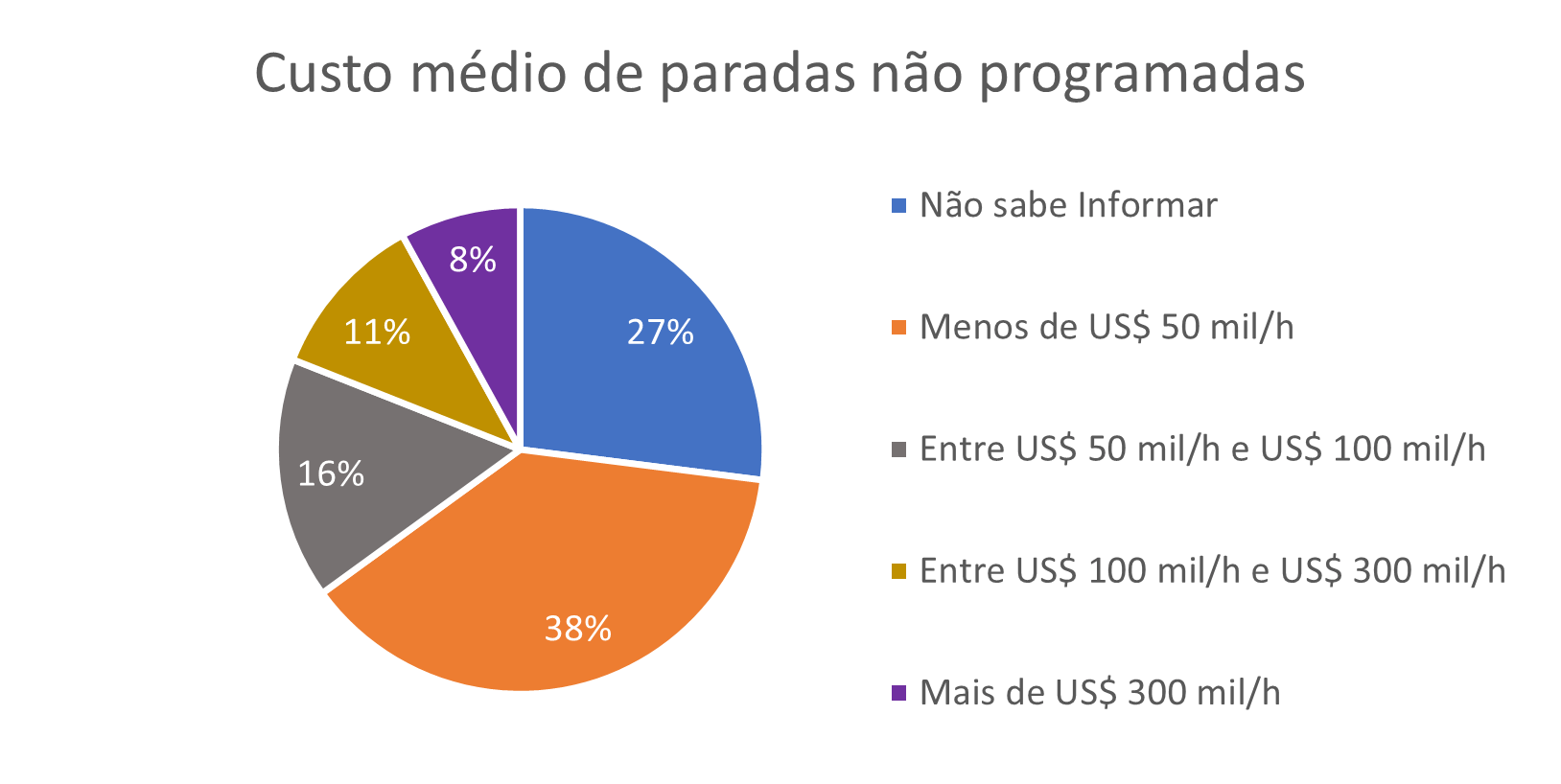
Esses prejuízos não se limitam ao escopo financeiro. Como efeitos colaterais, eles podem influenciar na gestão do fornecimento de recursos como energia, água de resfriamento e outros insumos. Podem levar a contaminação de outros equipamentos ou até do meio ambiente dentro e fora da unidade operacional.
Além disso, pode acelerar a depreciação do ativo e levar a acidentes, culminando em multas, diminuição da confiabilidade de consumidores e até perda de vidas.
Por fim, as paradas não programadas podem gerar consequências políticas e emocionais, incluindo o aumento do estresse de toda a equipe envolvida, a criação de conflitos entre responsáveis e executores, diminuição da reputação de líderes e desmotivação de funcionários.
Tudo isso aparece em diversos níveis de criticidade:
- Catastrófico (com perda de vidas e recursos ambientais)
- Crítico (com danos ao patrimônio)
- Marginal (com interrupções temporárias)
- Insignificante (que pode ser corrigido posteriormente)
A identificação dos riscos dessas paradas não programadas, na grande maioria das vezes, é feita através das atividades de inspeção que, por sua vez, fazem parte da rotina de todo ativo dessa indústria.
No entanto, o tratamento desses riscos ocorre de diversas formas, algumas mais reativas e outras mais proativas.
Reativas
Aceitação das consequências: o responsável reconhece o risco identificado, mas decide não investir de imediato na mitigação ou eliminação do risco. Por exemplo, um gestor decide não investir no reforço de um telhado que provavelmente apresentará infiltrações nos próximos 5 anos.
Reação às consequências: o responsável não faz planos e apenas reage, com surpresa, quando uma falha ocorre. Por exemplo: líderes se acusam mutuamente ao descobrir, de repente, infiltrações em um telhado e ninguém sabia que isso estava para acontecer.
Proativas
Agendamento das consequências: o responsável equilibra pressões sobre a gestão de ativos. Substituindo equipamentos obsoletos ou apenas justificando equipamentos antigos, mas que estão em boas condições. Por exemplo: um gestor precisa decidir se mantém um equipamento que está consumindo muita energia até estar esgotado ou agenda a substituição para usufruir mais cedo dos benefícios de um equipamento com maior eficiência energética.
Idade das consequências: o responsável substitui um equipamento quando ele atinge uma certa idade, definida em um calendário prévio baseado em estatísticas e vida média do equipamento em função das condições de uso. Por exemplo, dados sugerem que um equipamento tem uma estimativa de vida de 25 anos. Consequentemente, ao atingir o seu 24º ano, o responsável agenda a substituição do equipamento.
Condição das consequências: o responsável substitui o equipamento quando a sua performance deteriora em um certo limite. A substituição é justificada por um histórico de aferições de performance feitas ao longo do tempo. Por exemplo, um gestor define um escaneamento nos seus equipamentos feitos por sensores de temperatura por períodos regulares para detectar pontos quentes de risco e estabelecer quando trocar equipamentos.
É sabido que, em muitos casos, a substituição de equipamentos de forma reativa não é conflitante com a proativa. Mas, é importante que ela se mantenha em um percentual baixo. E, para que isso aconteça, torna-se necessário fomentar a capacidade de tomar decisões baseadas em dados que, por consequência, conduzir a companhia em direção ao incremento de soluções de alta tecnologia embarcada para a coleta e gestão desses dados referentes a todos os ativos.
No artigo “Os 6 estágios da indústria 3.0 até 4.0 (onde a sua empresa está hoje?)”, discutiu-se formas de avaliar o quanto de tecnologia uma determinada empresa usa nas suas operações e os benefícios decorrentes desse uso e, se identificadas oportunidades de melhoria, foram discutidos no artigo “A transformação digital da indústria de óleo e gás na gestão de ativos” diversos caminhos de evolução.
Mesmo assim, múltiplas abordagens para o mesmo problema suscitam redundância sadia e reafirmam a “história” contada pelos dados coletados no mundo real, os quais, invariavelmente, precisam ser interpretados e resumidos em painéis de indicadores e relatórios que, por sua vez, influenciarão decisões importantes. A melhor forma de observar o que está acontecendo em cada ativo pode estar na diversidade de soluções tecnológicas para a coleta e integração de informações.
Entra em cena o Sensoriamento Remoto e Imagens Orientadas
Como vimos no artigo “Ampliando segurança e eficiência na indústria de petróleo”, imagens de satélites, imagens de radar (SAR – Synthetic Aperture Radar) ou sonar, imagens e outros produtos produzidos por drones, AUVs (Autonomous Underwater Vehicles ou Veículos Submarinos Não-Tripulados) e ROVs (Remotely Operated Vehicles ou Veículos Operados Remotamente), além de vídeos e imagens orientadas, quando processadas e visualizadas de forma organizada e integrada, proporcionam visões únicas de riscos operacionais levantados em campo e da situação dos ativos, invisíveis em sistemas de gestão convencionais.
Com essas visões singulares, é possível ajustar o planejamento das atividades de inspeção e manutenção de forma mais assertiva, indo apenas aos pontos realmente relevantes, o que se reverte em eficiência operacional e redução dos custos da operação.
Na prática, é como visualizar os ativos a partir de múltiplos ângulos.
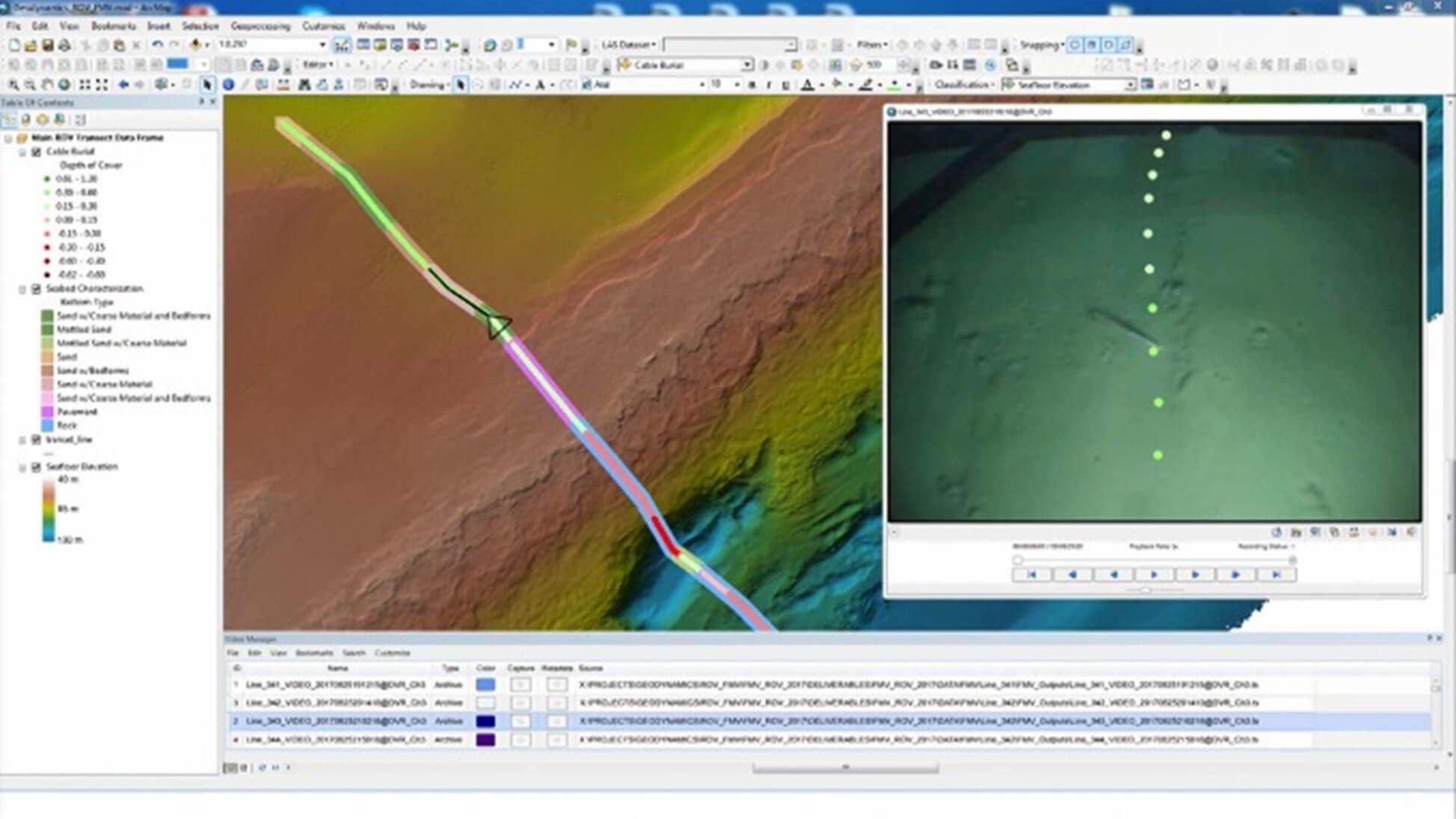
É comum empresas de Upstream Offshore contratarem serviços de inspeção por imagens e vídeo, seja pelo uso de ROVs, AUVs ou mesmo mergulhadores. Já as empresas de Upstream Onshore utilizam imagens e vídeos de drones, câmeras CCTV ou mesmo imagens registradas por colaboradores através de dispositivos móveis e equipamentos munidos de sensores específicos. Todos utilizam imagens de satélite (e, de forma mais rara, imagens de radar) para contextualização geográfica, identificação de riscos e execução de análises a cada nova necessidade.
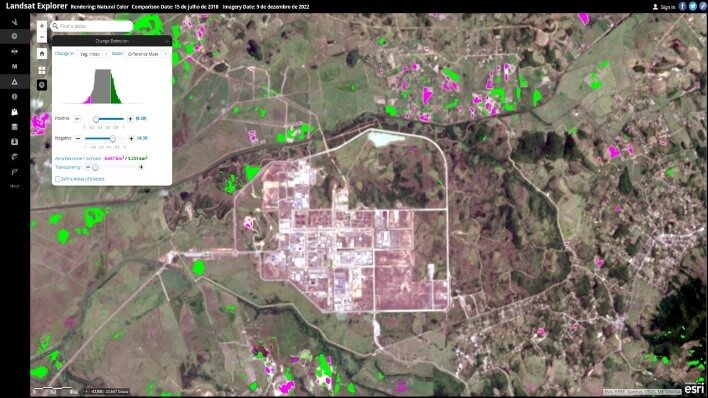
O mesmo ocorre com empresas de Midstream em suas faixas de dutovias ou cabotagem, além de empresas do Downstream em refinarias, petroquímicas e bases de distribuição de combustíveis.
Todas essas empresas já possuem fluxos de coleta, armazenamento e análise de todos esses dados. No entanto, todos esses processos costumam ser desestruturados, com coletas feitas por diversos tipos de equipamentos, catálogos feitos por planilhas eletrônicas ou sistemas isolados, armazenamento feito em sistemas de arquivos organizados manualmente e análise visual, desprendendo grande esforço de especialistas para extrair informação de valor.
Soluções ArcGIS como diferencial
Com as soluções ArcGIS, é possível extrair informação de valor de forma rápida e eficiente, organizando dados de diversos formatos em um banco de dados único que pode ser compartilhado de forma corporativa e acessado através de uma interface amigável de leitura universal: o mapa.
Além disso, as funcionalidades avançadas de análise e a integração com algoritmos conhecidos de inteligência artificial proporcionam formas automatizadas de identificação de riscos, diminuindo o tempo de análise visual por especialistas e aumentando a eficiência do processo.
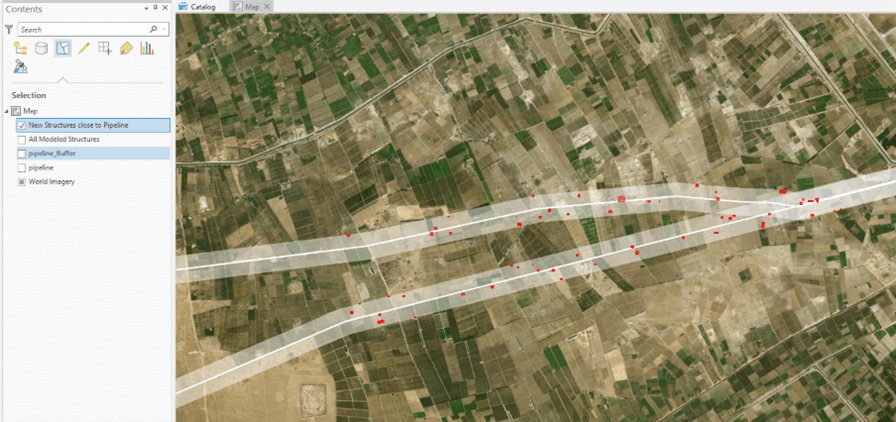
Por fim, painéis inteligentes fazem parte da solução e são criados praticamente sem a necessidade de programação, acessando diretamente todas as informações armazenadas e direcionando os resultados para indicadores customizados para cada necessidade.
No entanto, como isso acontece na prática? Qual ou quais métodos e recursos necessários para cada necessidade de negócio? Veja o nosso artigo “Segurança e Eficiência na indústria de óleo e gás com ArcGIS: Utilizando imagens de satélite, radar (SAR) e imagens orientadas no ArcGIS Pro e ArcGIS Enterprise para monitoramento de ativos” e tenha acesso a todos os detalhes!
[…] Para mais detalhes sobre essas soluções, veja o artigo Soluções GIS para Manutenção e Inspeção no Setor de Óleo e Gás. […]